Home >> Machinery >> Environment Engineering & Recycling Equipments >> Plastic Recycling Machine >> Details
PET Bottle Recycling Machine
PET Bottle Recycling Machine

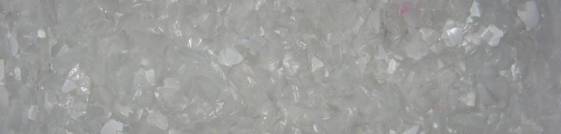
Capacity: 1500kg per hour (for reference, we can adjust the configuration according to your demand of capacity)
1. Label peeling off section
The labels of the PET bottles can be peeled off by the label peeling machine
2. Complete bottle washing section
The PET bottle after label peeling machine will be fed into the complete bottle washing drum by the conveyor. The PET bottle is washed according to the bottle washing technique requirement. The sediment and impurities inside the PET bottles will be pre-washed, and then also remove the residues, such as the trademarks of PE, paper labels and some PVC adhesive label which stays inside the PET bottles. More importantly, after being heated and pre-washed, the PVC bottles change in the physical property (comparatively with PET bottle, PVC bottle changes color to ivory white or light yellow). It is very easy to be selected by follow-up procedure.
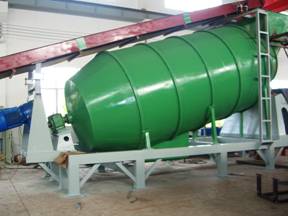
The washing process control and the washing detergent adding are controlled by the PLC computer automatically. According to the configuration of equipment, the washing water is 3 steps washing (for example, the first step washing, the second step washing with detergent, the third step washing is rinse).
3. Accumulating silo section and label blowing section:
The PET bottle after being washed by the complete bottle washing drum will be fed into a accumulating silo for water filtration, and then feeding into the label blowing machine by the conveyor, discharge the residue inside the PET bottles, such as the trademarks and garbage.
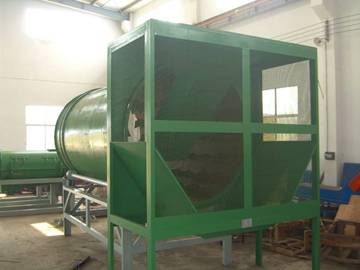
4. Manual sorting section:
Manual sorting section removes any other kinds of bottles from the PET bottles, such as, PVC bottle, different color bottles, label debris and garbage, etc. Ensure the transparent PET bottles for the next section. The sorting unit is divided into PVC bottle selecting post, different color bottles selecting post, label selecting post and garbage selecting post, etc. The practice has proved that if there is reasonable division of labor; establish the system of personal responsibility, the manual sorting effect could be better than automatic sorting machine effect.
During the bottle crushing, there are some caps and rings (the material of the caps and rings is PP or HDPE) should be removed. Based of the different density of different plastic (-1.3/ -0.8), water (the density is 1) is the medium. During the float-wash machine operation, the PET flakes sink, the floating caps and rings debris are removed, we can obtain more pure PET flakes.
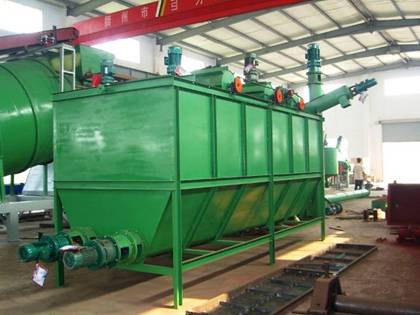
7. Hot washing, friction and rinse section
This section is to make PET bottle flakes more pure. It mainly relies on the three washing forces: mechanical, chemical and thermal power, after hot washing in the hot washing machine with detergent, after the friction of the high-speed friction machine, and rinsing with clean water in the rinse machining, completely remove impurities in the bottle flakes, such as glue, medicinal liquid and other impurities.
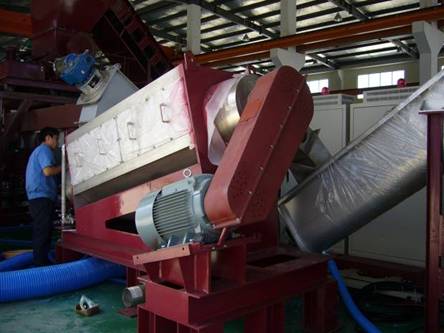
Hot washing machine
8. Dewatering and color separating machine and finished product storage section
This section will dehydrate the clean PET bottle flakes by the dewatering machine and by hot wind blower. There may be very small percent (less than 1.5%) of other color PET flakes inside the transparent PET flakes. We adopt one color separating machine which removes all of non-transparent PET flakes. The high quality PET bottle flakes (100% transparent) will be delivered to a silo. They are packaged by one automatic packaging machine.
This section will dehydrate the clean PET bottle flakes by the dewatering machine and by hot wind blower. There may be very small percent (less than 1.5%) of other color PET flakes inside the transparent PET flakes. We adopt one color separating machine which removes all of non-transparent PET flakes. The high quality PET bottle flakes (100% transparent) will be delivered to a silo. They are packaged by one automatic packaging machine.
9. Water circulation treatment system
The system includes the hot washing unit and washing unit water circulation system. The operation will be done in the closed-circuit system; the system configured with filtration and transportation facilities, to maintain the clean agent purity. Fill detergent liquid in time to maintain the clean agent concentration, and ensure the cleaning effect. The cleaning unit washing water can be reused, and it can lower the water consumption to the most economical level.
The system is to control the bottle washing equipment operation in accordance with the requirements and washing techniques. The equipments can be controlled both automatically and manually by the electrical system. And control the safety production.
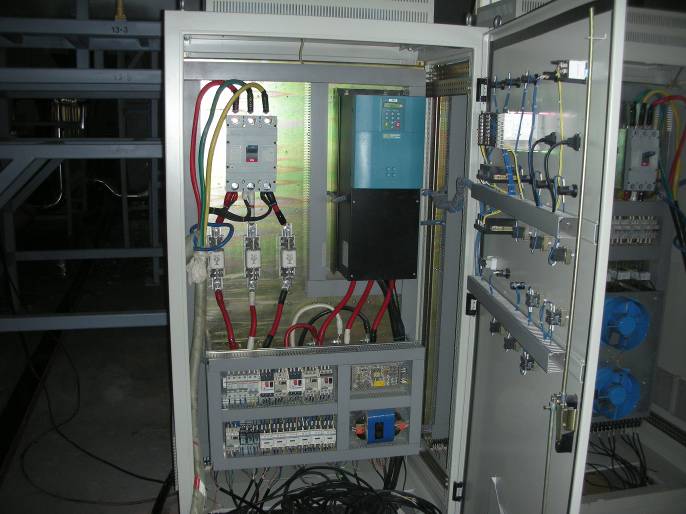
After the bottle pre-washing, selecting, crushing, float washing, hot washing, friction washing, rinsing and drying dehydration, color separating, the total content of impurities of PET bottle flakes is down to 100ppm, the PVC content is less than 30ppm. The washed high quality PET bottle flakes can be used to produce filament, chemical fiber, etc. high-grade plastic products.
|
Machine |
Quantity |
Usage |
1 |
Label peeling off machine |
1 |
PET bottle label peeling off |
2 |
Belt conveyor |
4 |
PET bottle transportation |
3 |
Belt conveyor |
1 |
PET bottle transportation to the washing machine |
4 |
Complete bottle washing machine |
1 |
bottle washing in accordance with the requirement of washing technology |
5 |
Double spiral conveyor |
1 |
PET bottle transportation |
6 |
Double spiral conveyor |
1 |
PET bottle transportation |
7 |
Label collection box |
1 |
PVC label collection from the label blowing machine |
8 |
Label blowing machine |
1 |
Blowing out the labels inside the PET bottles |
9 |
The wind blower for label blowing machine |
1 |
PVC label blowing |
10 |
Double spiral conveyor |
1 |
PET bottle transportation |
11 |
Selecting belt conveyor |
1 |
remove the heterogeneity bottles from the PET bottles, PVC bottle, different color bottles, label debris and garbage, etc. Ensure the clean PET bottles for the next section |
12 |
Selecting platform |
1 |
manual selecting platform |
13 |
Crusher |
1 |
PET bottle crushing |
14 |
Crusher platform |
1 |
crusher maintenance, the knives assembly and discharging |
15 |
Spiral conveyor |
1 |
PET bottle chip transportation to the float-wash machine |
16 |
Float-wash machine |
1 |
The PET chip sedimentation, remove the floating caps and rings debris, obtain the PET flakes purification effect |
17 |
Hot washing machine |
2 |
hot washing the PET flakes with detergent |
18 |
Spiral conveyor |
2 |
PET bottle flakes transportation to the friction machine |
19 |
Water circulation system of hot washing machine |
1 |
washing liquid recycling of the hot washing machine |
20 |
Friction washing machine |
1 |
PET bottle flakes friction washing, remove the glue and other impurities and wash the PET bottle flakes to clean |
21 |
Rinse machine |
1 |
Rinsing the PET bottle flakes to clean them totally |
22 |
Spiral conveyor |
1 |
PET bottle flakes transportation to the dewatering machine |
23 |
Dewatering machine |
2 |
PET bottle flakes drying dehydration |
24 |
Dehydration rinse trough |
2 |
filter impurities of the dewatering machine and the rinse machine |
25 |
Finished product silo |
1 |
PET bottle flakes storage |
The data are generally based on our previous successful project, we can adjust the specification according to your requirements.